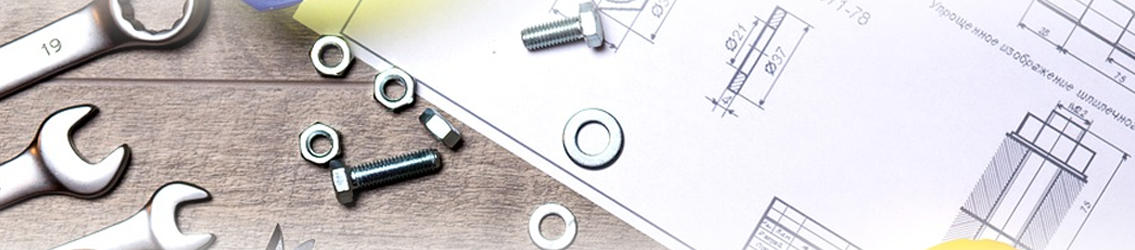
ANSI/IEEE
ANSI C62.45: Guide On Surge Testing For Equipment Connected To Low-Voltage AC Power Circuits
Standard Overview
ANSI C62.45 lists procedures for the performance of surge testing on electrical and electronic equipment connected to low-voltage AC power circuits, specifically using the recommended test waveforms defined in IEEE Std C62.41.2-2002. Nevertheless, these recommendations apply to any surge testing, regardless of the specific surges that may be applied. ANSI C62.45, the third document in a Trilogy of three IEEE standards addressing surges in low voltage ac power circuits, focuses on test procedures, using representative surge waveforms developed based on the two other documents of the Trilogy. There are no specific models that are representative of all surge environments; the complexities of the real world need to be simplified to produce a manageable set of standard surge tests. To this end, a surge environment classification scheme is presented in IEEE Std C62.41.2-2002.
Table 1: Summary of applicable standard and additional surge testing waveforms for Location Categories A, B, and C (Scenario I only) and for Scenario II
Download Standard
Table 1: Summary of applicable standard and additional surge testing waveforms for Location Categories A, B, and C (Scenario I only) and for Scenario II
Scenario I Surges impringing upon the structure from the outside and generated within |
Scenario II Direct lightning flash |
||||||
Location Category | 100 kHz Ring Wave | Combination Wave | Separate Voltage/Current | 5/50 ns EFT Burst | 10/1000 μs
Wave
|
Inductive Coupling | Direct Coupling |
A | Standard | Standard | — | Additional | Additional | Category B Ring Wave | Case-by-case assesment |
B | Standard | Standard | — | Additional | Additional | ||
C Low | Optional | Standard | — | Optional | Additional | ||
C High | Optional | — | Standard | Optional | — |
Download Standard
Products Used in Testing
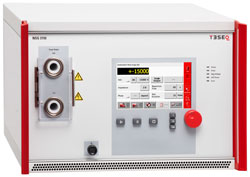
Teseq NSG 3150 Combination Wave Surge Generator | 15 kV
- Surge voltage up to 15 kV
- CDN range: Single & Three Phase, up to 63 A, 690 VAC, 1000 VDC
- Safest 15 kV connector type on the market
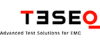
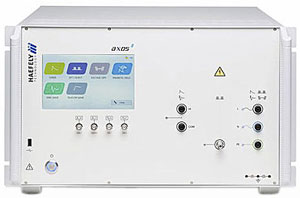
Haefely AXOS8 Compact Conducted Immunity Test System
- 0.2 – 5.0 kV ±10% at coaxial output
- 50 Ohms
- 5 ns ±30%
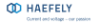
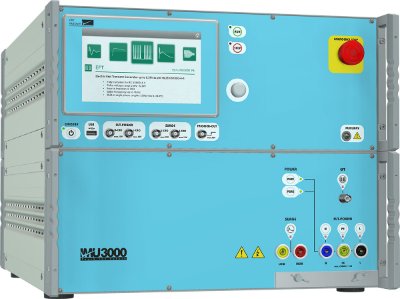
EMC Partner IMU3000 Immunity Tester
- 7” Colour touch panel
- Rotary knob for navigation and data entry
- EPOS (EMC PARTNER Operating System) a new concept in graphical user interface
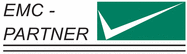
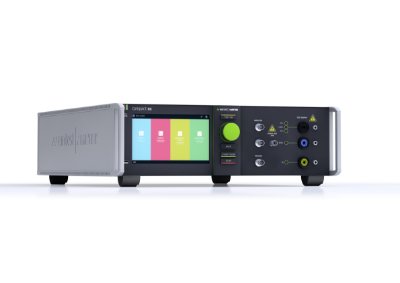
EM Test NX5 Multifunctional Test Generator
- Small transient generator with 7" color touch screen
- IEC 61000-4-4 | Burst testing, 5.5kV
- IEC 61000-4-5 | Surge testing, 5.0kV
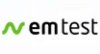
Related ANSI/IEEE Standards
Explore All StandardsANSI C63.2: American National Standard For Specifications Of Electromagnetic Interference And Field
ANSI C63.4: American National Standard for Methods of Measurement of Radio-Noise Emissions from...
ANSI C63.16: American National Standard Guide For Electrostatic Discharge Test Methodologies And...
ANSI/IEEE C37.90: Standard for Relays and Relay Systems Associated with Electric Power Apparatus
ANSI/IEEE C37.90.1: Surge Withstand Capability (SWC) Tests for Relays and Relay Systems...
ANSI/IEEE C62.41: IEEE Recommended Practice on Surge Voltages in Low-Voltage AC Power Circuits
ANSI/IEEE C95.1: Standard for Safety Levels with Respect to Human Exposure to Radio Frequency...
Related Product Solutions
Explore All Solutions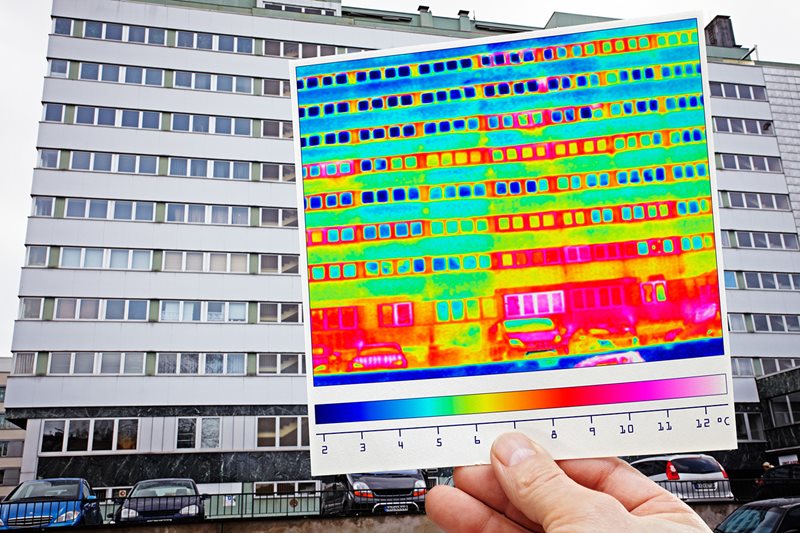
Building Envelope Testing
Building envelope testing is the process of testing the physical separator between the interior and exterior of a building to determine if there are any air, water, or thermal leaks within the structure. The building envelope consists of all parts of the outer exterior that keep the building environment dry, heated, or cooled for climate control.
Building Envelope Leaks & Contamination
Many different intrusions can result from an improperly built or maintained building envelope, such as air intrusion, water intrusion, and thermal intrusion. Leaky roofs are a common source of water and water vapor leakage, which can damage walls. Water infiltration is particularly harmful to any building’s structural integrity because it can cause extraordinary damage and remain undetected for a while. Many of these building code problems can be addressed by adhering to the standards established by the NIBS, the ASTM and the AAMA.
Moisture and Water Analysis
Moisture control is imperative to maintaining a building’s structural integrity, as well as quality health and safety standards. Therefore, waterproofing is necessary to prevent water damage to a building’s foundation. Air barriers must also be in place to prevent unnecessary ventilation and drafts in the building. Any HVAC system installed must be designed specifically for the purpose of air pressure testing.
Building Forensics
Building forensics also discover damage to a structure and determine possible causes using scientific processes. These tests investigate the materials, products, compounds, and structures that either fail or do not operate as intended. Failures can cause injury or damage to property, which are often costly and time-consuming.
Building Envelope Testing
Building envelope testing plays a crucial role in maintaining environmental health and safety. Universities, corporate campuses, healthcare, hospitals, medicine, and military bases
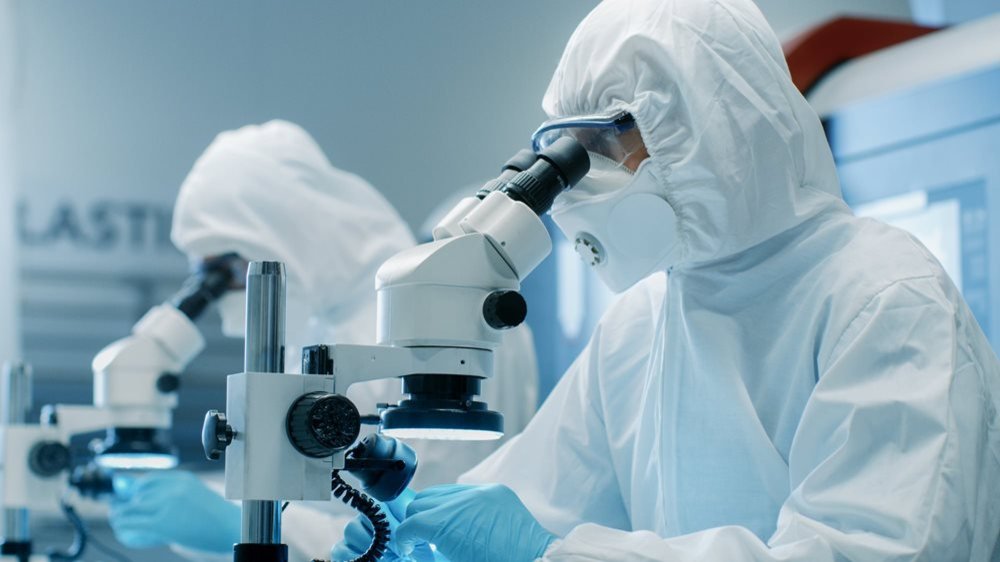
Clean Room Testing
Testing your clean room is essential to achieve contamination-free research and manufacturing as well as efficient operation and financial saving. Manufacturers of semiconductors, flat panel displays, and memory drives have extremely high requirements, and biotech and pharmaceutical companies, medical device manufacturers, healthcare facilities and other organizations that produce, store and test their products are regulated by law. The sensitive technologies handled in clean rooms require careful vigilance—a single speck of dust, for example, has the potential to destroy a semiconductor’s microscopic electronic components. To maintain a controlled environment, clean rooms are pressurized with filtered air, regulated by ISO, IEST and cGMP standards, and tested annually with the following methods and equipment.
Clean Room Testing Equipment
Particle Counters
The measurement of particles in the air is essential to a clean room setting. Particle counters are the ideal tool; these highly sensitive devices index how many particulates of a specified sizes are present. Most counters can be adjusted to the allowable threshold of the particle sizes. Ensuring the clean room always meets standards requires the installation of a continuous monitor particle counter that is always running. This practice is essential to maintaining a controlled environment and protecting products or equipment from contamination. The process of how particle counting should be performed is defined in ISO 14644-3.
Portable particle counters can be utilized for continuous monitoring, but they and handheld particle counters are typically used in the authentication and confirmation of the continuous monitoring counter and in localizing the source of particles. A variety of manufactures, including Particle Measuring Systems, Fluke, and Met One, supply clean room particle counters with top models like:
Particle Measuring Systems Lasair III 110
Beckman
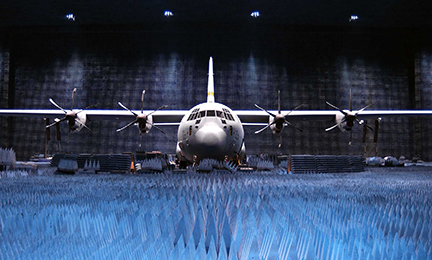
What is EMI/EMC Testing?
EMI/EMC testing indicates to engineers whether a device is compatible with its electromagnetic environment as well as whether it will produce electromagnetic interference (EMI) in real-world situations. In a world without testing, the risk of helicopters falling out of the sky, respirators going silent, or your cell phone losing its signal would increase. All of these machines rely on technology which can be disrupted by rogue electromagnetic energy, and thus undergo EMC testing with the appropriate equipment to fulfill requirements standards dictated by IEC, CISPR, and MIL-STDs and achieve EMI compliance.
ATEC explains what EMC is, the test methods and their standards, and some of the instruments that perform each type of test. Keep reading to learn more.
What is EMC?
Electromagnetic compatibility, commonly referred to as EMC, is a branch of electrical engineering focused on EMI/EMC testing. Jets, gaming systems, and automobiles, for example, all need to be configured to protect against harmful electromagnetic interference, or EMI. Products themselves may also emit electromagnetic interference and must avoid crossing signals. A device which interrupts cell tower signals or damages airplanes could cost companies millions in fines or lawsuits—and such incidents did happen before the consequences of EMI were widely known.
For the details on EMI specifically, read our blog What is Electromagnetic Interference?
EMI/EMC Testing Procedure
Find the Standards. “Which standards apply to my product?” is the first question you should ask yourself. Varying between product type and geography, standards can be difficult to define or pin down and missing an EMC standard can be disastrous for manufacturers. Contact an EMC lab and determine which standards you need to meet before sending your product in or develop a plan yourself if you’re familiar with the requirements. To do your own research, visit
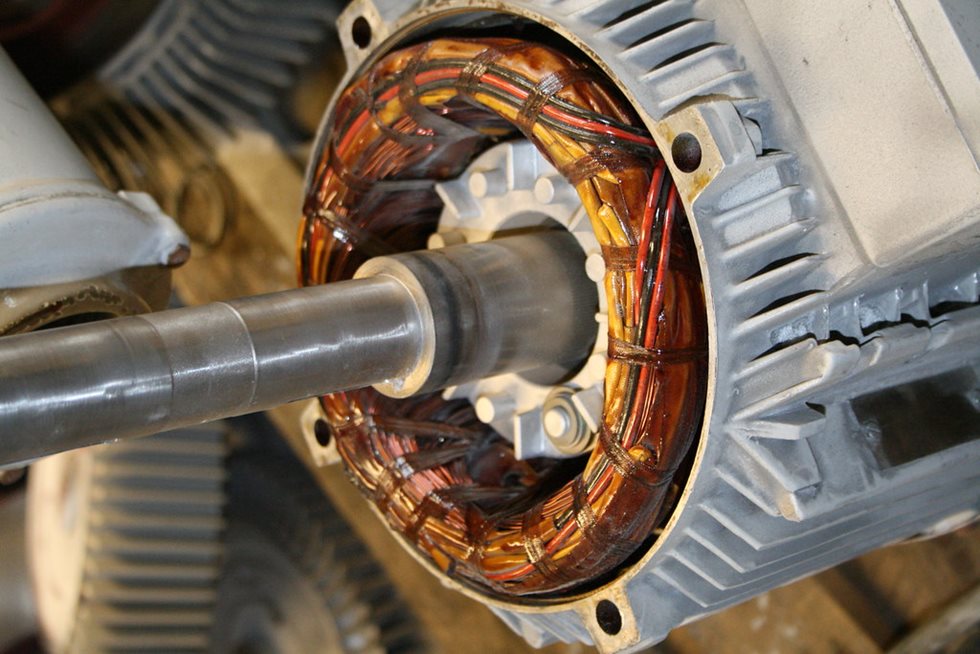
Laser Alignment
Achieving shaft alignment is a perennial task in machinery maintenance: roughly half of all machinery fails due to some degree of misalignment and requires connecting shafts to be tested and re-aligned. Alignment measurements can be performed with a feeler gauge, calipers, straightedge or dial indicator(s), but laser shaft alignment offers the distinct advantages of portability along with unrivaled speed and precision measurement.
How To Use A Laser Alignment Tool To Test Rotating Equipment
Perform pre-alignment check
Perform rough alignment
Eliminate obvious soft foot
Tighten bolts
Perform final soft check
Mount sensors to stationary and movable shafts or hubs
Turn on lasers
Follow on-screen prompts
Enter dimensions
Select tolerances
Perform readings, 3 measurement points
Correct for both horizontal and vertical misalignment
Watch the following video for a step-by-step shaft alignment performed with the Vibralign Fixturlaser EVO:
What Is A Laser Shaft Alignment Tool?
A laser shaft alignment tool performs measurements by means of two sensors mounted on two connected shafts. Both sensors fire a laser beam and receive the other sensor’s beam simultaneously; a comparison of the beams reveals whether the shafts are aligned and within a specified tolerance. The data then appears on a display unit, tablet or PC, allowing for analysis and correction to be performed.
Considered to be on the cutting edge of dimensional analysis in the world of manufacturing, laser alignment tools are vital allies to test engineers charged with mechanical reliability. Laser beams are free from the laws of gravity, immune to bracket sag and eliminate coupling anomalies. A laser shaft test system can rotate to compensate for coupling anomalies, calculate precise values for horizontal and vertical (shimming) corrections, and can even measure more than two machines, all in the same
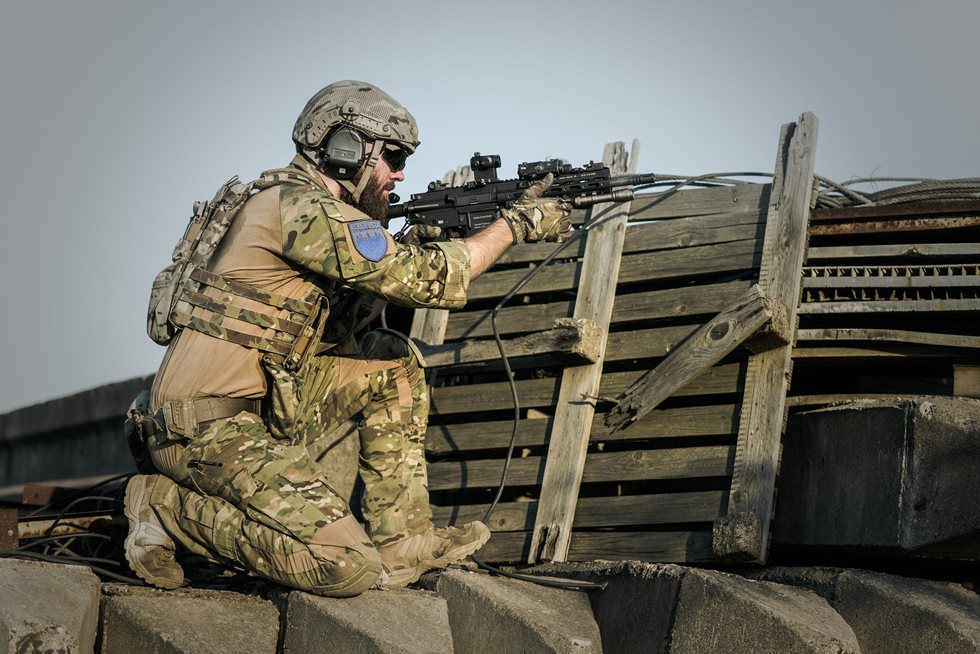
MIL-STD Testing
Walking into a military compound like marine corps base Camp Pendleton in San Diego, north of ATEC’s corporate headquarters, few civilians imagine what thorough testing each piece of technology they encounter undergoes. Jeeps humming along in the distance are lightning-proof after undergoing indirect lightning testing. Inside a laboratory, walls tested by sound level meters offer refuge from noise pollution. Military testing standards pervade every part of military life; even the ground below a marching unit holds tested machinery, the piping beneath the troops’ feet carefully measured by flow meters.
What is a MIL-STD?
In the military, testing is crucial to the safety and efficiency of operations. Manufacturing is regimented like any other faction of military life, and engineers navigate a labyrinth of testing requirements for their products to emerge from the bunkers of R&D ready to operate under fire. Electromagnetic interference, or EMI, for example, could pierce a weak point on an M1-Abrams tank if untested for its susceptibility to rogue electromagnetic emissions. Countless other pieces of military equipment would fail in the line of duty, too, if it were not for the safeguards of military manufacturing: MIL-STDs.
MIL-STDs, or military standards, are requirements approved by the U.S. Department of Defense that engineers must conform to when developing and testing military technology. Standardization encourages defense contractors who supply government goods to craft safe and efficient products, and many times commercial manufacturers ensure their products undergo EMC testing as well. A smartphone which can withstand the blistering desert heats of Afghanistan is considered to be well-qualified to serve civilian needs.
Types of MIL-STD Testing
To meet a certain military standard, engineers need to acquire specific equipment to achieve compliance. Advanced Test Equipment Rentals (ATEC) is an ISO/IEC 17025 accredited test