The True Cost of Site Downtime and Why Testing Often is So Important

An unfortunate reality of working with machinery and equipment – no matter how advanced – is that the risk of issues, disruptions, or flat out equipment failure is always present. Routine maintenance will help prevent and mitigate a number of these risks, but even then, sometimes things just happen. If you put off testing your electrical system for hidden issues, you may wind up with an outage and some downtime. Even if your factory production halts for just one hour, the consequences can be grave. Here's why.
Downtime directly impacts your revenue. It causes you to bleed
out money. Even if you can’t keep production moving, you aren’t absolved from paying production costs. Overhead, wages, overtime – you’re still responsible for all of this, regardless of whether or not you are producing. One hour of downtime can cost you thousands of dollars in lost revenue. And unless you're incredibly smart, lucky, or some combination of the two, you probably won’t be able to make that back.
To illustrate this, let's say you operate a facility that produces widgets. Maybe you can produce 1,000 widgets per hour, and each widget generates $10 of revenue. When production is running without fault, you can generate $10,000 over the course of an hour. If your production costs to manufacture widgets round out to be roughly $4,000 an hour, then your income during production is $6,000. But if you suffer an outage, electric fault, or any other issue that results in downtime – that's $6,000 an hour, gone. Even if your plant can't produce during that time, you are still responsible for fixed costs, like overhead and wages. You may also have to pay for additional labor and overtime, or lose money on materials that need to be scrapped and replaced. Add all of that to your bill, and you owe a lot of people money by the time the hour is up. What's left over for you?
Testing for the integrity and functionality of your
electrical system is crucial, and must be done often. Even if you feel that you're being overly cautious, or too prudent – it's so much better (and cheaper) in the long run to spend a small amount on test equipment and labor than it is to burn money in the event of downtime. During routine maintenance, you should test to make sure your system isn't suffering transient voltage, operational overloads, shaft imbalance, and more. Tools like power quality analyzers can diagnose transient voltage (we recommend the Fluke 437 Three Phase Energy & Power Quality Analyzer). Infrared cameras and digital multimeters will determine whether or not your motor is under excessive duress and risks overloading. A vibration tester will identify shaft imbalances that are the result of manufacturing variations, uneven mass in motor windings, and other wear-related factors.
Protect your plant against downtime, and save yourself from the staggering costs, too. Use facility power and industrial electrical equipment to monitor and identify issues before they go from minor to massively expensive. For more information on how to select the right electrical equipment to prevent downtime in your facility, please feel free to contact our electrical team leads.
Downtime directly impacts your revenue. It causes you to bleed
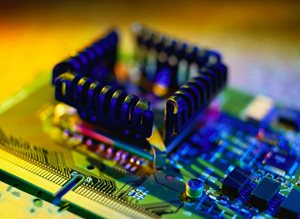
To illustrate this, let's say you operate a facility that produces widgets. Maybe you can produce 1,000 widgets per hour, and each widget generates $10 of revenue. When production is running without fault, you can generate $10,000 over the course of an hour. If your production costs to manufacture widgets round out to be roughly $4,000 an hour, then your income during production is $6,000. But if you suffer an outage, electric fault, or any other issue that results in downtime – that's $6,000 an hour, gone. Even if your plant can't produce during that time, you are still responsible for fixed costs, like overhead and wages. You may also have to pay for additional labor and overtime, or lose money on materials that need to be scrapped and replaced. Add all of that to your bill, and you owe a lot of people money by the time the hour is up. What's left over for you?
Testing for the integrity and functionality of your
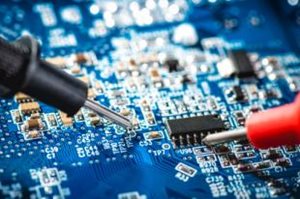
Protect your plant against downtime, and save yourself from the staggering costs, too. Use facility power and industrial electrical equipment to monitor and identify issues before they go from minor to massively expensive. For more information on how to select the right electrical equipment to prevent downtime in your facility, please feel free to contact our electrical team leads.
Posted May 31, 2017