Substation Maintenance
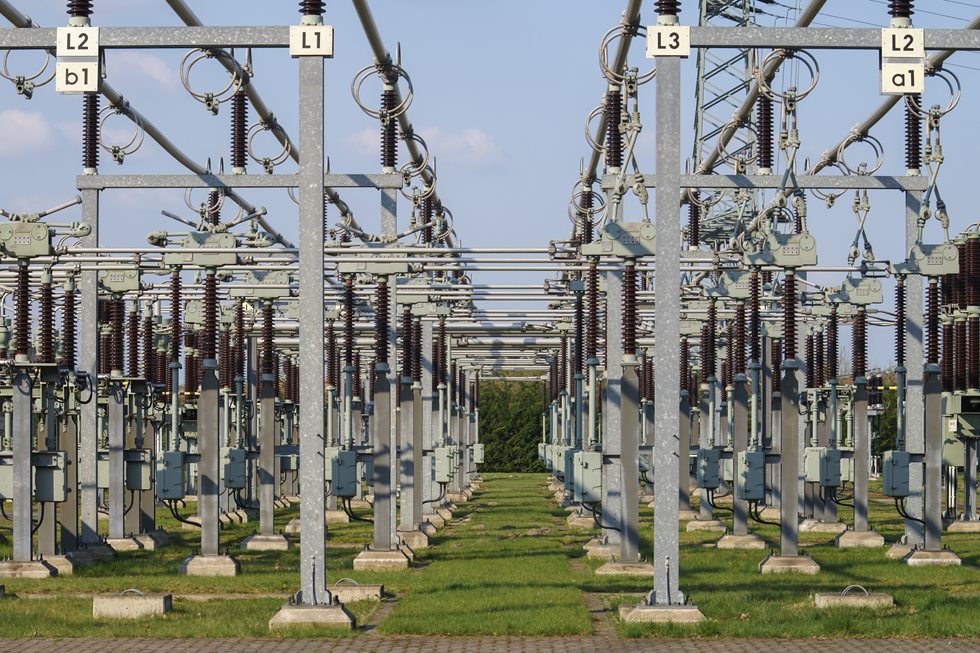
Substations convert our energy from hundreds of thousands of volts to manageable levels. Once transformed, energy can be safely channeled along cables to our homes and places of work. To supply us with the precise amount of voltage for powering our appliances without shorting out systems, however, a substation needs to achieve seamless interaction between its components, notably transformers, circuit breakers and protective relays. A failure in even one element of the system may lead to grid collapse—meaning a whole neighborhood goes dark. Testing the elements of a substation is an essential practice engineers conduct numerous times over a substation’s operating lifespan, and can be generally divided into the following phases.
Relevant Standards: ANSI
Relevant Standards: IEEE C37 and IEC 62271.
Relevant standards: ANSI C37.90, IEC255-4, IEC60255-3, and IAC.
Substation Testing Procedures
- Factory Acceptance Tests (FATs)
- Factory acceptance tests occur in the pre-installation phase and verifies that the components created for the substation meet design and function requirements before delivery and integration into the system. Acceptance testing generally includes one unit of each type to be incorporated into the system. Adhering to the supplier/buyer contract is paramount to the success of acceptance testing; these tests, after all, are intended to confirm to the buyer that the components are crafted correctly.
- Commissioning
- Commissioning is the next round of testing the electrical parts will undergo before service. Manufacturer data will be cross-checked, products will be looked over for transportation damages and wiring will be replaced in refurbishment projects. Existing parts with shorter lifespans will be renewed while others remain, and the interaction between old and new parts will be assessed.
- Best Commissioning Practices
- Test the system comprehensively; most effective after testing individual components and not neglecting any critical points
- Achieve .9999999 or “seven-nines” availability, which translates to a down time of three seconds a year
- Utilize load banks to ensure the transformers have sufficient current. Avoid using customer-provided loads, which may prove faulty
- Test the entire protection system, as engineer may need to bypass the protection system at some point for load testing
- To test distance relays, apply a reactive load
- Results can be benchmark for future testing – develop a maintenance/testing program after commissioning to establish continuing success
- Best Commissioning Practices
- Commissioning is the next round of testing the electrical parts will undergo before service. Manufacturer data will be cross-checked, products will be looked over for transportation damages and wiring will be replaced in refurbishment projects. Existing parts with shorter lifespans will be renewed while others remain, and the interaction between old and new parts will be assessed.
- Maintenance Tests
- Maintenance testing is conducting annually or once every three years as part of an overall substation inspection, and along with electrical tests includes a thorough cleaning, substation inspection, wire replacement and troubleshooting. Unplanned outages are commonly caused by meters, relays, busses and racking mechanisms, parts which a maintenance test should be analyzing. Site Acceptance Tests (SATs) will be performed as a kind of initial maintenance testing, evaluating the electrical compatibility of the parts in a system, this time on a live grid.
Substation Test Equipment
Transformers, circuit breakers and protective relays, the essential components of substations, each require distinct types of instruments to test them. A transformer reduces the power flowing into a substation and a circuit breaker will safely switch off the power during shortages or other dangerous energy fluctuations. Relay systems trip circuit breakers when faults are detected.Transformer Test Equipment
A transformer converts a generally high input to a lower output, transforming a primary current into a secondary current of an appropriate power level for sending the current into the residential and commercial worlds. Transformer testing verifies the important qualities of a transformer, notably that the output, or secondary current, requires precise amplitude, polarity and phase for accurate protection and controlled metering. Measuring the phase and ratio displacement, magnetization curve and winding resistance are a few other factors transformer testing will reveal.Relevant Standards: ANSI
- Current Transformer Test Sets
- A current transformer test set identifies transformer faults which may lead to the primary current overwhelming the insulation which safeguards against short circuits. Sets often include saturation, radio, secondary winding testers and more, and meet IEEE or IEC standards.
- Winding Resistance Meters
- Winding resistance meters diagnose resistive connections, partial blowouts, shorted windings and a variety of other wiring aberrations. By measuring the voltage of and current traveling along the wire, operators can determine the resistance of any sort of motor including transformers, chokes, heart coils and generators.
- Turn Ratio Test Sets
- A transformer turn ratio test set reveals shorted turns or, in some cases, open-circuit conditions, by measuring the ratio of high voltage to all other winding. Then a turn ratio kit will display the recorded variations in ratio, optimally falling within .5% of nameplate.
- Power Factor Test Sets
- Power factor test sets are used to conduct power factor and tan delta testing with a goal of maintaining the ratio of resistive components to capacitive components, known as the tan delta ratio. Years of use brings with it risk of exposure to dirt and moisture, which leads to the formation of conducted paths leaking electric current.
Circuit Breaker / Switchgear Test Sets
Circuit breakers safely switch off currents to prevent shortages, outages and the general havoc. A transient or severe fluctuation in current can wreak an electrical system. Circuit breaker testing assesses several key parameters to circuit breaker functionality, including resistance, timing, minimum pick-up, travel and power factor. A circuit breaker should allow for energy to flow with minimum possible loss when it is not tripped and should be checked for corrosion or oxidation due to temperature or humidity stressors.Relevant Standards: IEEE C37 and IEC 62271.
- Circuit Breaker Test Sets
- A circuit breaker test set determines if a circuit breaker will trip and the switchgear will be activated, halting current overflow and redirecting power to the rest of the electrical system.
- Primary / Secondary Current Injection Test Sets
- Primary current injection test sets insert a strong current on the primary side of circuit breakers, allowing for testing of the trip mechanism, wiring and current sensors. Secondary current injection test sets are inserted directly into the trip relay, focusing solely on whether the current is cut off. Circuit breakers respond to these injection tests by either tripping and ending the current, or failing, and allowing the current to continue to travel into the electrical system.
Relay Test Sets
A protective relay will detect minor fluctuations in voltage, resistance, current or even temperature that could spell disaster for the people relying on a substation. Once a relay finds a fault is developing, it trips the circuit breaker. The power shuts off; people and electrical facilities are safe. Relay testing will prove the relay logic settings and functions are working “as set,” ensuring the relay is true to its name.Relevant standards: ANSI C37.90, IEC255-4, IEC60255-3, and IAC.
- Protective Relay Test Sets
- Protective relay test sets will simulate changes in voltage, resistance and current to test whether a protective relay is operational or could allow energy or insulation fluctuations to go undetected and thus allow excess amounts of energy to pass.