NDT | Non-Destructive Testing
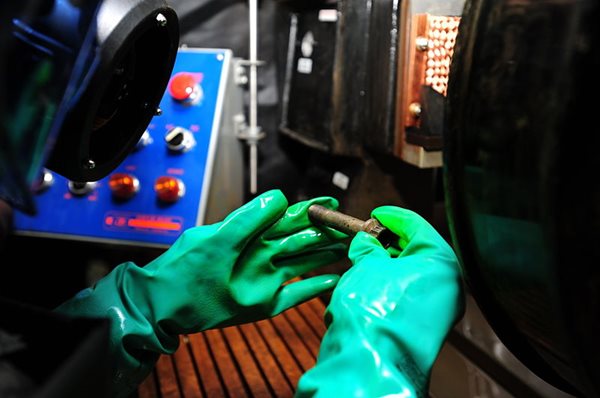
What is NDT?
Non-destructive testing, or NDT, is the inspection of an object without physically damaging or altering its properties.
NDT testing is typically performed to diagnose the functionality, proper installation and maintenance, and makeup of an object. Non-destructive tests evaluate both the external and internal composition of objects under test, determining everything from the dimensions of an object to its roughness or vibration levels. Non-destructive techniques identify structural faults through non-invasive testing methods by harnessing the power of ultrasonic, infrared, visual inspection and laser technology, among others. NDT testing saves money and time, reducing production costs by preserving the subject under test and allowing engineers to experiment with several testing parameters before returning to research and troubleshooting.
What is the ASNT?
Engineers look to the American Society for Nondestructive Testing (ASNT) for NDT personnel qualification and certification practices. When selecting an engineer to perform NDT on your product, machine or facility, refer to the following standards to verify their ASNT compliance:- SNT-TC-1A
- Guidelines for developing your own in-house NDT certification program; includes recommended skill levels for all tiers of NDT qualification, including training/experience hours and examination eligibility.
- ANSI/ASNT CP-189
- Establishes the minimum standards for qualifying/certifying NDT personnel. An American National Standard which differs from the “recommended practices” of SNT-TC-1A by detailing hard requirements rather than educated suggestions.
- ANSI/ASNT CP-105
- Outlines training for Level I and Level II personnel as well as topical outlines of Level III qualifications. Details minimum training courses for each.
- ANSI/ASNT CP-106
- An adoption of ISO 9712:2005 which describes certification requirements for engineers to conduct the following: Electromagnetic Testing (ET), Magnetic Particle Testing (MT), Liquid Penetrant Testing (PT), Radiographic Testing (RT), Ultrasonic Testing (UT) and Visual Testing (VT)
- ANSI/ASNT ILI-PQ-2010
- Focuses on the requirements for certifying in-line inspection (ILI) personnel who will be evaluating pipes and pipelines.
What is ASNT Certification & Qualification?
To perform NDT testing, technicians and engineers need to follow the general requirements established by EN ISO 9712 and other quality standards. Inspectors themselves must certified as well, acquiring central third-party certification in compliance with EN ISO 9712 by a certification body accredited by ISO IEC 17024.- Level 1: Technicians First level NDT inspectors are qualified to perform certain calibrations and tests under close supervision, following specific instructions for testing and what criteria contribute to rejection.
- Level 2: Engineers Level 2 personnel set up and calibrate test equipment and conduct NDT themselves, testing according to industry-specific codes and standards. Engineers with Level 2 certification are then entrusted to report on results, documenting the evaluation process and confirming passes and rejections.
- Level 3: Specialized Engineers Engineers with Level 3 certification direct laboratories, establishing measurement techniques and certifying personnel. Level 3 NDT personnel specialize in the non-destructive testing process, possessing intimate knowledge of both the science behind the testing and the rigors associated with conforming to ANST-associated standards and philosophy.
Why is NDT Important?
- Accident Prevention. Ensures products, equipment and facilities are safe for the public. Employers with the foresight to rent infrared cameras and conduct building envelope testing, for example, could avoid the corrosion of structural members in an old building, which could be ripe with potential lawsuits in case of a collapse or dangerous mold contamination.
- Reliability. Non-destructive testing assesses the reliability of a device or system, empowering project managers to make informed decisions on repairs, remodels and replacements. A flow meter will indicate to facility managers whether a new piping system is a financially sound investment or whether the current system is dependable, perhaps saving thousands of dollars.
- Meeting Standards. NDT fulfills requirements for numerous organizations, including the following and more:
- American Society of Testing and Materials (ASTM)
- American Society of Mechanical Engineers (ASME)
- American Petroleum Institute (API)
- American Welding Society (AWS)
- Aerospace Industries Association (AIA)
- International Organization for Standardization (ISO)